Keep Truckin!
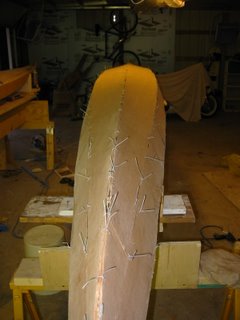
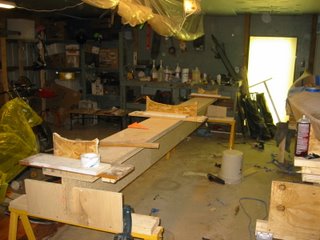
I have to say that this is an exciting part of the build, as I have not seen the boats in any other positions than the one I began the build in. I took the time tonight to fillet the hull plates on the outside, the first round anyway. Tomorrow, if the epoxy hardens, I ill remove the stitches and begin sanding. With the cold night expected tonight however, I suspect thy will need anothe day.
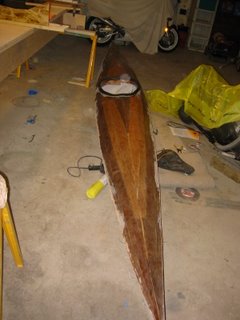
But I have planned or that, as I have the coaming ready to be built on the other yak tomorrow. So either which way I am putting in a few solid hours tomorrow.
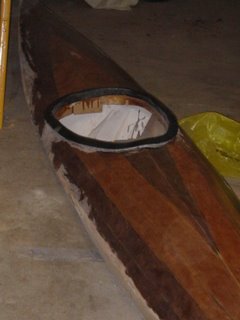
Last, I have to say moving the Kayak to the floor for the station change was very cool. I haven't even realized how nice the okum and sappelle contrast each other untli tonight. Also seeing the boat in a more natural setting was motivating. Sometimes you loose steam in a project this size, but all it takes is a change of scenary to keep truckin!